It might sound like a redundancy stating the obvious, but constructability has become a core value in today’s construction industry. But what does this really mean?
As a project management approach, constructability brings the processes of building a structure fully into the building’s design. What it involves is to create a complete map of the construction process from start to finish prior to actual commencement of the project.
The idea is to identify challenges that might affect the plan before a project begins, to anticipate problems and prevent errors, and to avoid unnecessary delays, and cost overruns.
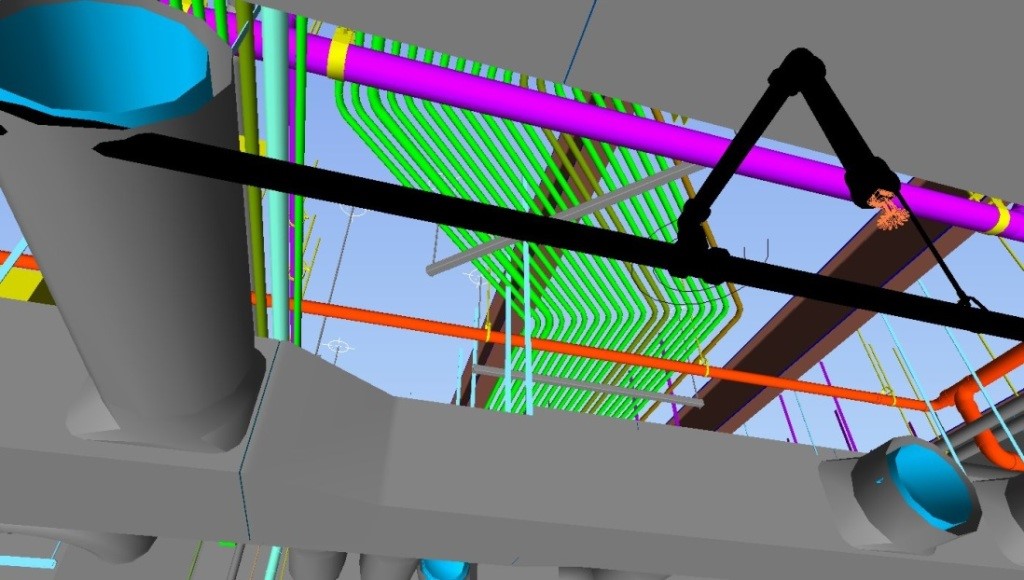
Perhaps no segment of the construction community is more heavily dependent on constructability than the subcontractors who belong to the fraternity of MEP. Delivering the HVAC, electrical power, communications and plumbing, the MEP systems providers operate at the very center of the construction value chain. The capabilities they deliver enable the finished facility to perform perfectly as planned for its owner and tenants.
In particular, the mechanical and electrical contractors find themselves sharing the very tight spaces assigned to building operations and infrastructure. With their work buried in walls, or suspended within narrow ceiling space or occupying subflooring or the slab, electrical and HVAC systems have to “play well” together in the finished building. To optimize schedules and avoid conflicts in narrow spaces, MEP providers have become experts in building information modeling (BIM) to assure the constructability of their contributions.
Designing Construction Processes into the Plan
More than ever time is money, which means continually pursuing smarter, faster and less costly methods of building increasingly sophisticated structures, such as hospitals and laboratories. By paying exacting attention to placements, modeling supported in the field by GPS-driven Trimble® technology enables the constructors to achieve the most cost effective execution, time after time with fewer exceptions or deviations.
What’s just as important to the process is bringing construction knowledge into conceptual planning, so that design and the physical resources needed for flawless execution can be reconciled in advance to realize project objectives within the best possible time frame. Not once, but again and again, over the course of a multiphase project. For example, in many cases, we’re able to apply the model with prefabrication to build complex, repeatable assemblies in advance, off-site in a safer, controlled fabrication environment. Thus with prefab we’re able to take constructability to new levels of productivity, while protecting both the construction process and the schedule from the impact of unforeseeable changes.
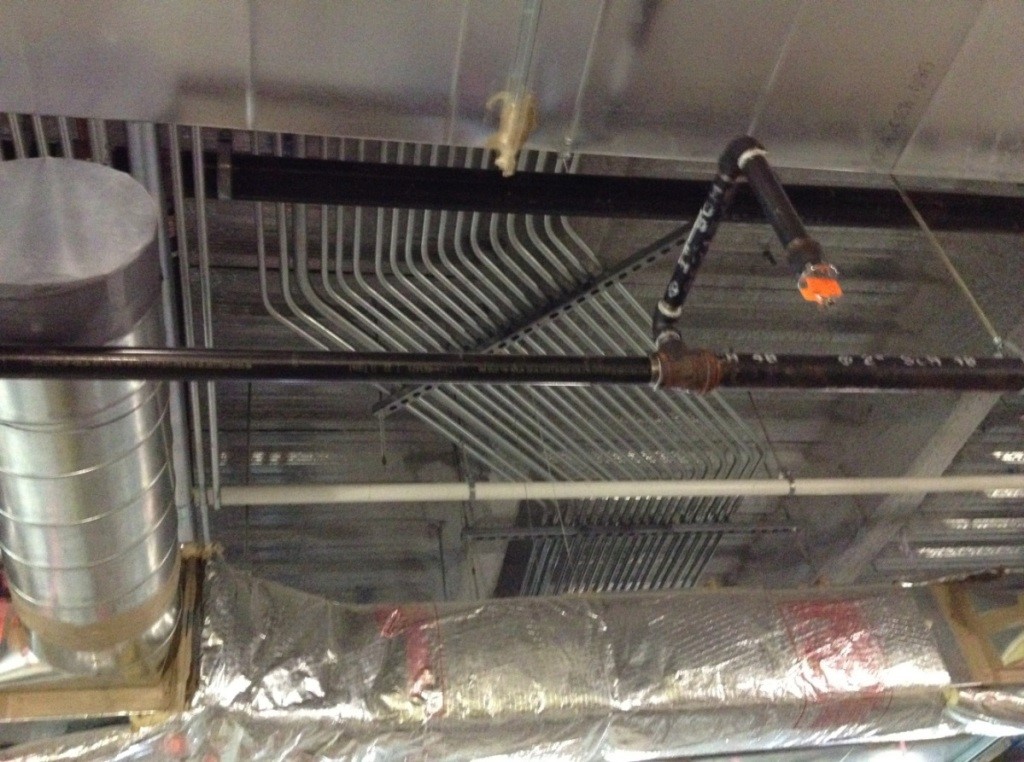
Constructability, then, is all about improving planning and listening between the trades and so that the design and the processes of execution are optimized with timely three dimensional instructions for the crews. This helps to assure repeatable efficiencies with which structures can be built. In the end, it means bringing construction knowledge related to project delivery processes into the design to assure thereby that project goals are achieved at the best possible price, so that everyone on the construction team can share in the success of the owner.